
生産システムの改善事例集/Ⅵ.ピッキングシステム設計のポイント
1 生産ラインにおける順建てシステム導入によるコストダウン
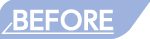
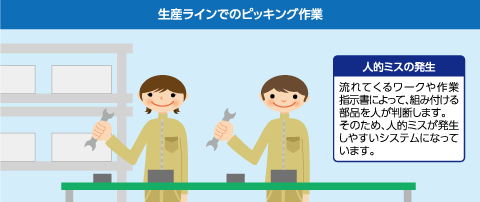
従来のピッキングシステムでは、ワークに組付ける部品が部品棚に収納されているために、生産ラインのピッキング作業にスペースが必要となっていました。流れ作業で行われるピッキング作業では、ワークの変更や工程変更を行う場合、部品棚の設置位置やレイアウト変更に工数がかかっていました。さらに、人の判断による部品取り出しの為、組み付け間違いが発生していました。
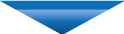
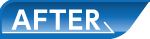
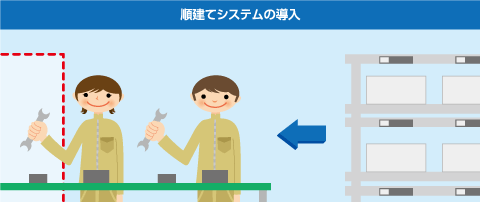
生産ラインに順建てシステムを導入する事により、生産ライン内に配置する部品棚を減らすことが可能となり、作業工程変更も容易になります。また予め、生産の順番に部品を整列させる自動搬送システムを組むことも可能になる為、作業効率も改善され、生産ライン全体を短く・シンプルにできます。サイクルタイムの短縮や歩留まりの改善に大きな効果があります。